Сталь після гарту: структура та властивості
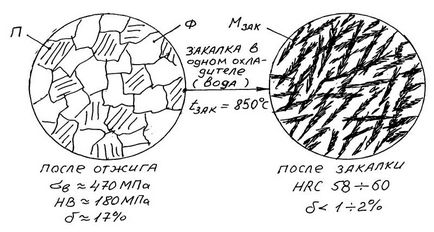
Мікроструктура стали 45 після відпалу і загартування
Загартування: сутність операції
- легованих (вони виробляються відповідно до вимог ГОСТ 4543);
- підшипникових по ГОСТ 801;
- рессорно-пружинних по ГОСТ 2052 і ГОСТ 14959;
- всіх типів інструментальних, як легованих, так і нелегованих.
Щоб зрозуміти ефективність загартування, необхідно звернутися до структури стали після виплавки і подальшої гарячої прокатки на потрібний режим - смугу, пруток або спеціальний профіль (куточок, швелер тощо).
Будь-яка сталь має кристалічну структуру, яку становить безліч кристалів. Якщо лити сталь з подальшим охолодженням розплаву, то ці кристали перетворюються в багатогранні освіти, звані зернами. Оскільки при цьому відбувається активне насичення киснем, між суміжними кристалами виникають порожнечі, які в процесі охолодження злитка поступово заповнюються сірої, фосфором і іншими легкоплавкими неметаллическими включеннями. Це не тільки знижує пластичність (фосфор і сірка - дуже тендітні хімічні елементи), а й сприяє появі досить грубих скупчень зерен, що робить метал нерівномірним по своїй щільності. Обробляти такі вироби неможливо - злиток почне розколюватися. Тому відразу після виплавки виконується прокатка, в ході якої вихідні дефекти заліковуються, і структура стає більш однорідною. Відповідно, збільшується щільність, а також зникають поверхневі тріщини.
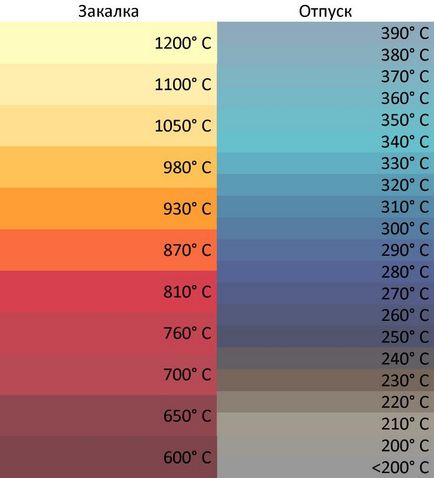
Температура заготовки в залежності від кольору при нагріванні
Пластична деформація позитивно впливає тільки на макроструктуру. За зміну мікроструктури відповідає гарт - сукупність технологічних методів термічної обробки, суть яких полягає в збільшенні міцних показників стали. Сенс гарту полягає в тому, щоб зафіксувати ряд високотемпературних складових мікроструктури (надають стали стійкість) для звичайних умов експлуатації виробів. Відповідно, сталь, не змінюючи свого хімічного складу, різко підвищить рівень своїх деяких механічних характеристик:
- межі тимчасового опору σв. МПа;
- границі текучості σт. МПа;
- межі втоми σі. МПа;
- твердості по Бринеллю HB або Роквеллу НRC.
При цьому деякі показники - зокрема, ударна в'язкість, відносне подовження, - після гарту стають нижче. Якщо це критично з точки зору подальшої експлуатаційної стійкості деталі (а в більшості випадків так і відбувається), то правильно після її гарту виконати ряд додаткових операцій: відпустка, старіння та ін.
Температурні зміни в структурі
Загартування проводиться досить часто для продукції, виготовленої з якісних конструкційних сталей, що містять більше 0,4% С, і практично завжди - для конструкційних легованих сталей, оскільки саме для них зазвичай і пред'являються підвищені міцнісні вимоги.
Вибір режиму гарту залежить від призначення деталі. Найбільш поширені такі технології:
- Термообробка маловуглецевих конструкційних сталей (менше 0,2% С), для яких необхідне поєднання поверхневої твердості з досить вузький серцевиною. У цьому випадку спочатку виконують цементацию - насичення поверхні додатковою кількістю вуглецю, а вже потім сталь гартують;
- Термообробка середньовуглецевих сталей з 0,3 ... 0,6% С. Вони застосовуються для виробництва відповідальних машинобудівних виробів складної форми, які працюють в умовах знакозмінних навантажень. Нормалізація завжди виконується після гарту;
- Хіміко-термічна обробка, яка виконується щодо високолегованих сталей, де глибинні шари можуть залишатися в'язкими. Основні варіанти виконання такої обробки - ціанування, нітрідірованіе, сульфурірованіе - виробляються також після гарту.
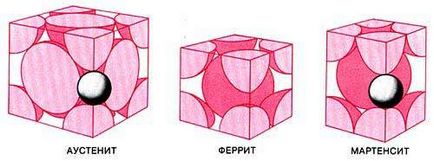
3 форми кристалів заліза в сверхвисокоуглеродістие стали
- У діапазоні температур до 723 ° С - ферит і перліт (перліт представляє собою механічну суміш фериту і цементиту, куди підмішуються і карбіди легуючих елементів).
- Вище цієї температури і до 850 ... 900 ° С суміш фериту з аустенітом, причому область стійкого існування структури залежить від відсотка вуглецю, і поступово знижується від діапазону 950 ... 723 ° С до 0.
- Нижче цієї температурної лінії структура є вже чисто аустенитной.
Для відображення динаміки структурних змін в конструкційних сталях при їх нагріванні широко застосовується відома діаграма «залізо-вуглець», по якій встановлюють режими загартування і наступного відпуску. Часто тут же наводяться і фотографії структурних складових.
режими загартування
Оскільки при загартуванню ростуть не тільки міцності, а й крихкість, технологія правильного ведення процесу полягає в тому, щоб, з одного боку, зафіксувати так можна більшу кількість залишається аустеніту, а іншого боку, знизити негативні прояви таких змін. Особливо це важливо для деталей складної форми, де вже є концентратори напружень.
Загартування підрозділяється на наступні види:
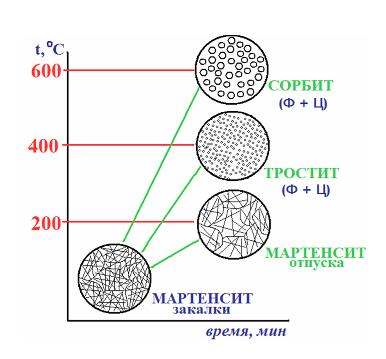
Три види відпустки після гарту
Особливості загартування інструментальних сталей полягають в тому, що вони працюють при набагато підвищених експлуатаційних навантаженнях: наприклад, для важко навантажених інструменту вони досягають 3000 ... 3500 МПа. Тому вкрай важливо забезпечити задовільний поєднання всіх параметрів міцності. Принциповою відмінністю всіх режимів гарту інструментальних сталей є обов'язковість відпустки безпосередньо після гарту.
Найкращий результат дають такі режими загартування:
- Изотермическая.
- Загартування з мимовільним відпусткою, при якій нагріту деталь короткочасно витягують з охолоджувальної середовища (масла), очищають від утворилася плівки окислів, після чого знову опускають в масляну ванну.
- Чистий, при якій нагрів ведуть в печах з контрольованою атмосферою, вільної від окислів.
- Світла, коли продукція нагрівається в лужних розплавах.
Якщо ви знайшли помилку, будь ласка, виділіть фрагмент тексту і натисніть Ctrl + Enter.