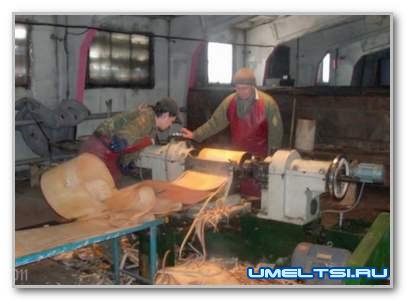
При будівництві моделей часто доводиться застосовувати шпон різної товщини. Зазвичай потрібну товщину отримують шліфуванням за допомогою грибка з наклеєною на торці шкіркою, вставленого в патрон дриля. Такий спосіб найдоступніший, але він має ряд недоліків: низька продуктивність, неможливість обробити шпон товщиною менше 0,5 мм, оскільки через обертання грибка шпон виривається з рук і ламається, і, нарешті, основний недолік - це велика забрудненість повітря деревної пилом . Обробити більше трьох-чотирьох пластин не вдається навіть у респіраторі.
Всіх цих недоліків позбавлений сконструйований мною шліфувальний верстат, що працює за принципом зустрічного фрезерування. Він був виготовлений (за винятком зварювальних робіт) в умовах авіамодельної лабораторії. У його конструкції відсутні дефіцитні деталі і матеріали.
Всі вузли верстата кріпляться на підставі, що представляє собою паралелепіпед розмірами 200x265x340 мм, зварений із сталевих куточків 40x40x4 мм. До основи приварюються, крім того, два кронштейни, виготовлені з швелера № 8, для кріплення корпусів підшипників барабана.
Барабан (основний робочий орган) і його шків - литі. Як матеріал використаний алюмінієвий сплав АЛ-25, з якого зроблені поршні автомобільних двигунів. Поршні розплавляються в муфельній печі, а потім відливаються в піщану форму. Отвори в барабані під поворотний болт-затиск шкурки і протівовесний болт повинні бути просвердлені симетрично щодо його осі. До речі, маса у першого (разом з «собачкою» фіксатором) і маса другого повинні бути рівні. В іншому випадку в результаті дисбалансу виникне вібрація, яка приведе до передчасного зносу підшипників і відіб'ється на працездатності верстата.
Корпуси підшипників виконані звареними. Остаточний розмір під підшипники в корпусах розточується після зварювання. Барабан приводиться в обертання за допомогою кліноременниє-ної передачі від електродвигуна потужністю не менше 300 Вт, з числом оборотів в хвилину від трьох до п'яти тисяч, з досить великим пусковим моментом, так як барабан має досить пристойну масу, незважаючи на те, що він виконаний з алюмінієвого сплаву. Цій вимозі відповідають колекторні електродвигуни. Я використовував на верстаті мотор від побутового електрополотёра.
Принципово важливим у пропонованій мною конструкції шліфувального верстата є наявність системи відсмоктування забрудненого тирсою і деревної пилом повітря. Ця система робить верстат екологічно чистим і більш «комфортабельним» при роботі, так як дозволяє обійтися без респіратора. Для відсмоктування тирси використаний відцентровий вентилятор-нагнітач системи опалення салону автомобіля, який встановлюється на різьбовому кінці осі барабана. Такий «пилосос» по продуктивності не поступається побутовому агрегату.
Кожух вентилятора кріпиться до кронштейну підшипника за допомогою гвинтів-баранчиків, що дозволяють швидко знімати його, коли виникає необхідність замінити зношених шкурку. На постачання патрубок надаватися мішечок з щільної тканини для збору тирси. Всмоктуючий отвір кожуха вентилятора з'єднується з порожниною кожуха барабана за допомогою патрубка. Патрубок виклеюють з склотканини на пенопластовой болванці, яка потім виплавляється ацетоном. Порожнина кожуха барабана утворена двома концентричними оболонками, прикріпленими до торцевих пластин-фланців. Внутрішня з них може бути приварена переривчастим швом, а зовнішня - обов'язково суцільним, щоб уникнути втрат тиску. Відстань між оболонками вибирається з умови рівності площі отвору всмоктування кожуха вентилятора площі двох щілин, утворених оболонками. У передню щілину всмоктуються тирса, що викидаються барабаном при шліфуванні, а в задню - тирса, які захоплюються шкіркою і викидаються відцентровою силою барабана.
Кожухи барабана і пасової передачі і обшивка підстави верстата виготовлені з сталевого листа товщиною 1,5 мм. Ось барабана виточена зі сталі 30, а інші деталі - зі сталі 10.
Операція по заправці шкурки проста і досить наочно показана на малюнку. Натяжка шкурки здійснюється за допомогою ричага- «собачки», надягнутого на квадратну частину поворотного болта-затиску шкурки і фіксується в одному з п'яти положень.
Стіл виготовляється із сталевого листа товщиною 10 мм і має розміри 180x350 мм. Його робоча поверхня повинна бути рівною, по можливості відшліфованою на пласко верстаті. Стіл, шарнірно закріплений на підставі, піднімається і опускається за допомогою регулювального болта, що дає можливість отримувати шпон товщиною від 0,3 до 30 мм. Необхідний розмір встановлюється по лінійці, пригвинченої до основи. Лінійка градуюється за допомогою мірних брусків, затискаємо між барабаном і столом.
Про непоганий продуктивності верстата красномовно свідчить той факт, що за один прохід можна знімати «стружку» товщиною до 1,5 мм.
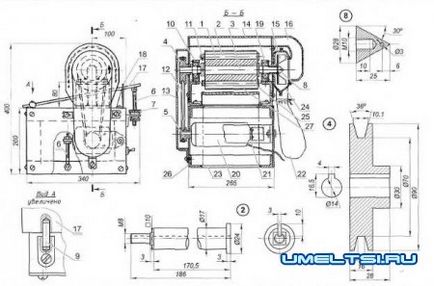
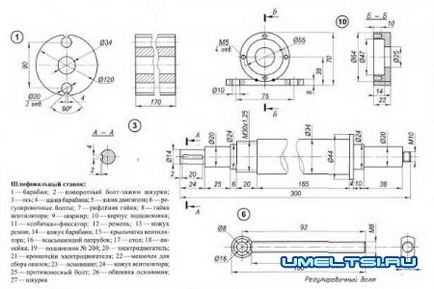
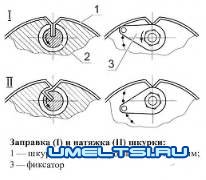