Примітка. Для приводу від поршневих двигунів значення слід збільшити на 50-70%.
Муфта з пружною оболонкою (рисунок 11.10) характерна тим, що в якості пружного елементу використовується гумова оболонка, що нагадує автомобільну шину. Для полегшення складання іноді застосовують роз'ємну, що складається з двох половин оболонку або замінюють останню декількома пружними хомутами, що мають таку ж форму перетину.
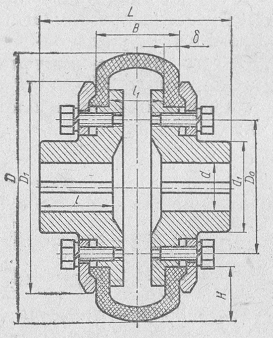
Рісунок11.10 - Муфта з пружною оболонкою
Гумова оболонка має велику пружністю, що надає муфті високі компенсуючі властивості: осьовий зсув від 3 до 6 мм, радіальне - від 2 до 6 мм і кутове - від 2 до 6 €. Крім того, одна полумуфта може обернутися щодо іншої на кут до 30є.
Умова міцності оболонки на зрушення в перерізі близько затиску:
де Мр - розрахунковий момент, Нмм;
- окружна сила в перерізі близько затиску, Н;
- діаметр окружності в перерізі близько затиску, мм;
- довжина кола, мм;
τ - товщина оболонки, мм;
Н / ММІ - допустиме напруження на зрушення для матеріалу оболонки.
У таблиці 11.6 наведені основні розміри муфт з пружної оболонкою.
Таблиця 11.6 - Основні розміри муфт з пружної оболонкою, мм
Особливості мастила редуктора
У місцях сполучення рухомих деталей механічних передач неминуче виникають сили тертя, на подолання яких витрачається частина переданої корисної потужності. Кращим засобом, що дозволяє різко знизити негативну дію сил тертя, є мастило сполучених деталей і вузлів мастилами та мазями. В окремих випадках, коли механізм довгий час знаходиться в бездіяльності (в резерві, ремонті і т. Д.), Змащують не тільки місця сполучень, а й всі деталі і поверхні механізму, що піддаються корозії (зазвичай технічним вазеліном або гарматної мастилом). У закритих передачах мастило деталей, як правило, проводиться безперервно, а у відкритих - періодично. Мастило сприятливо впливає на роботу зачеплень, пом'якшує удари в зубчастих і інших передачах, знижує шум і нагрів механізму під час роботи і захищає відкриті місця деталей від корозії. Підбір сорту масла і його якості є серйозним завданням, від .правільності вирішення якої багато в багатьох випадках залежить нормальна робота механічної передачі.
Найважливішими властивостями мастил є жирність і в'язкість. Олійністю називають здатність мастила прилипати до поверхні металу, що забезпечує, зокрема, освіту на поверхнях, що труться суцільною і міцною адсорбированной плівки.
В'язкістю масел називається сила взаємного зчеплення між окремими частинками, що визначає здатність масла чинити опір переміщенню і витискування його із зазорів між твердими поверхнями. Розрізняють в'язкість динамічну і кінематичну.
Ставлення динамічної в'язкості масла до його щільності при тій же температурі називається кінематичною в'язкістю.
У приладобудуванні широко поширене застосування рослинних масел (лляне, рицинова і ін.), А також масел тваринного походження (кісткове, спермацетове). Найбільш поширене касторове масло, яке має високу жирність і значну в'язкість. Масла тваринного походження мають більш високу олійністю, але малою в'язкістю.
Ці масла часто застосовують для змащення точних приладів і механічних передач дуже малої потужності (годинникові механізми, самописні прилади і т. Д.).
Якщо подача рідкого масла на поверхні, що труться утруднена, для змащення цих вузлів використовують консистентні мастила, складені з мінеральних масел з невеликими добавками рослинних або олій тваринного походження. Загущення цієї суміші досягається шляхом добавок до неї кальцієвого або натрового мила.
В умовах роботи механічних передач малої потужності для змащування поверхонь тертя застосовують як рідкі, так і консистентні мастила (мазі), при цьому мастило повинна бути нейтральна, т. Е. Не повинна діяти на метал хімічно і не створювати умови для утворення корозії і за своїми фізичних і хімічних властивостях стійка на тривалий час.
Рідкі олії застосовують при високих кутових швидкостях машини і при великому діапазоні температури навколишнього його повітря, наприклад, масло приладове, яке має температуру спалаху в закритому тиглі не нижче 120 °, а температуру застигання не вище -60 ° С. Разом з цим необхідно враховувати, що рідкі масла мають і суттєві недоліки. Так, наприклад, в зв'язку з швидким витіканням масла з місць сполучення деталей, необхідне застосування сортів олії, що мають велику жирність або застосування більш складних ущільнюючих пристроїв.
Консистентні мастила зазвичай закладають в корпус вузла при його складанні і складних ущільнень не вимагають.
Зміна мастила проводиться значно рідше, приблизно один раз за 6-8 місяців. Добавка мазі проводиться за допомогою шприца через прес-маслянки або маслянки ковпачкового типу.
З консистентних мастил для шарикопідшипників найбільшого поширення в приладобудуванні отримали мастила ГОІ-54, ЦИАТИМ-202, ОКБ і суміші з різних співвідношень масел ГОІ-54 і МВП. З маловязких масел найбільше застосування знаходить приладове вазелінове масло МВП і спеціальні мастила ОКБ і ВНИИНП.
У механічних передачах найбільш ретельно доводиться здійснювати мастило деталей, що обертаються, зубчастих або інших видів зачеплень, при цьому вимоги до мастильних матеріалів як в першому, так і в другому випадках різні.
Визначення мінімального обсягу масла в редукторі
Мінімальний обсяг масла знаходиться за наступною формулою:
Вибір електродвигуна, кінематичний розрахунок і схема приводу. Частоти обертання і кутові швидкості валів редуктора і приводного барабана. Розрахунок зубчастих коліс редуктора. Витривалість зубів по напруженням вигину. Розрахунок обертаючих моментів вала.
Кінематичний розрахунок приводу. Вибір потужності двигуна, передавальних відносин приводу. Визначення оборотів валів, обертаючих моментів. Термін служби приводного пристрою. Вибір матеріалу зубчастого колеса і шестерні. Підбір муфти, валів і підшипників.
Проектування прямозубого редуктора. Вибір електродвигуна приводу. Розрахункове напруження згину в небезпечному перерізі зуба шестерні. Конструктивні розміри зубчастих коліс і елементів корпусу. Основні параметри зубчастої пари. Орієнтовний розрахунок валів.
Твір розрахунку потужності електродвигуна, кінематичних параметрів вала (частота обертання, кутова швидкість), визначення конусного відстані, ширини вінця, модуля передачі, зовнішнього діаметра коліс з метою проектування конічного редуктора.
Порядок проектування конічного редуктора, кінематичний і силовий розрахунок приводу. Проектний розрахунок конічної зубчастої передачі, валів, колеса, корпуса і кришки редуктора, його ескізна компоновка. Вибір деталей і вузлів, їх перевірочний розрахунок.
Визначення механічних властивостей матеріалів електродвигуна, розрахунок параметрів передачі. Конструювання валів редуктора: розрахунок діаметрів валів, шпонкових з'єднань і креслення вала редуктора. Розрахунок швидкохідного валу і підбір підшипників кочення.
Розрахунок клинопасової передачі. Потужність на ведучому валу. Вибір перетину ременя. Оцінка помилки передавального відношення. Кінематичний розрахунок редуктора. Передавальне відношення черв'ячної передачі. Вал черв'ячного колеса редуктора і підбір підшипники кочення.
Вибір електродвигуна і силовий розрахунок приводу. Розрахунок закритою циліндричної зубчастої передачі. Уточнений розрахунок валів на статичну міцність. Визначення розмірів корпусу редуктора. Вибір мастила зубчастого зачеплення. Перевірочний розрахунок шпонок.
Проведення розрахунку передавального відносини, швидкості обертання валів з метою вибору електродвигуна. Визначення допустимих контактних напружень зубчастих коліс, розмірів корпусу редуктора, тихохідного і швидкохідного валів. Особливості збирання редуктора.
Кінематична схема ходового механізму екскаватора. Визначення геометричних розмірів зубчастих коліс і їх кінематичних параметрів. Розрахунок потужності на валах механізму. Визначення крутних моментів на валах передачі. Проміжний вал редуктора.
Визначення передатного відношення і розбиття його по щаблях, окружних і кутових швидкостей зубчастих коліс і крутять моментів на валах з урахуванням ККД. Матеріал і термообробка зубчастих коліс. Кінематичний і геометричний розрахунок зубчастої передачі.
Постановка завдання розрахунку вала. Визначення сили реакцій в підшипниках, епюри на стислих волокнах. Побудова епюри крутних моментів. Визначення сумарних реакцій в підшипниках, їх вантажопідйомності по найбільш навантаженої опорі і його довговічності.
Розрахунок терміну служби приводу. Кінематичний розрахунок двигуна. Вибір матеріалу зубчастої передачі. Визначення допустимих напружень. Розрахунок навантажень валів редуктора. Проектний розрахунок валів. Ескізна компоновка редуктора. Конструювання зубчастого колеса.
Методика проектування трехступенчатого циліндричного редуктора. Порядок визначення допустимих напружень. Особливості розрахунку 3-х ступенів редуктора, проміжних валів і підшипників для них. Специфіка перевірки міцності шпонкових з'єднань.
Вибір конструкції редуктора. Дані для проектування. Вибір електродвигуна і кінематичний розрахунок. Попередній розрахунок валів редуктора. Конструктивні розміри шестерні і колеса. Перевірка довговічності підшипників і міцності шпонкових з'єднань.
Розробка приводу стрічкового конвеєра: вибір електродвигуна; розрахунок зубчастих передач, підбір і перевірка на придатність шпонкових з'єднань, підшипників; проект загального вигляду черв'ячного редуктора; вибір матеріалів; виконання робочих креслень деталей.
Залізовуглецеві сплави - стали і чавуни, як найважливіші металеві сплави, їх хімічний склад і основні компоненти. Фази в залізовуглецевих сплавах. Властивості і використання цементиту. Структурні складові в залізовуглецевих сплавах.
Характерні групи сплавів сталей при кристалізації, їх основні властивості, температури плавлення і кристалізації. Твердофазні перетворення в сталях. Побудова кривої охолодження і зміни мікроструктури при кристалізації маловуглецевої сталі.
Розробка приводу стрічкового транспортера, що складається з електродвигуна, клинопасової передачі і двоступеневого циліндричного зубчастого редуктора. Кінематичний і силовий розрахунок приводу. Форма і розміри деталей редуктора і плити приводу.
Кінематичні розрахунки, вибір електродвигуна, розрахунок передавального відношення і розбивка його по щаблях. Призначення матеріалів і термообробки, розрахунок допустимих контактних напружень зубчастих коліс, що допускаються напруг вигину, розмірів редуктора.