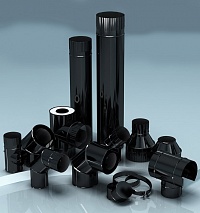
Особливості та переваги емальованому продукції
Емалі - тонкі стеклообразниє покриття (фініфть, стеклоемаль), що наносяться на вироби з металів та їх сплавів і закріплюються випаленням. Характеризуються високою твердістю, корозійну стійкість, зносо- і жаростійкістю. За призначенням емалі поділяють на технічні та художні, за зовнішнім виглядом - на прозорі і непрозорі (тушковані), білі і кольорові.
Технічні емалі наносять на вироби з чавуну, сталі, алюмінію і сплавів легких металів. Поділяють їх на грунтові і покривні. Грунтові емалі, що містять 50-60% SiO2, 2-8% А12О3, до 30% В2О3, 12-30% Na2О, 4-10% СаО і ін. Оксиди (до 10 найменувань), наносять на вироби першим, грунтовим шаром, який добре зчіплюється з металом. Для посилення зчеплення з металом вводять так звані оксиди зчеплення - Со2Оз, Ni2O3, MoO3.
Покривні емалі, що наносяться на грунтові, підрозділяють на непрозорі (білі, пофарбовані) і прозорі (безбарвні, пофарбовані). Вони містять ті ж оксиди, що і грунтові, і, крім того, SnO2, Sb2O5, ZrO2, TiO2, фториди лужних металів, які виконують роль глушників (іноді емалі класифікують саме по складу глушників). До складу забарвлених емалей входять також пігменти (оксиди Мn, Сu, Со, Сr, Ni), люмінофори та ін.
Технологія виробництва емалей включає: складання шихти, що містить різні стеклообразующие матеріали (кварц, кварцовий пісок, сода, поташ, крейда, польовий шпат, глина, каолін, бура) і спеціальні добавки (див.вище); плавлення шихти [для фріттованних (попередньо сплавлених) емалей] при температурі 1150-1450 ° С до отримання скляних гранул; розмелювання гранул до отримання пудри (помел без води) або стійкого шликера (помел з водою і змішування з єднальними компонентами). Стійкий малов'язкі шликер зазвичай містить 30-40% по масі води, 5-10% глини, 0,1-0,5% електролітів (сода і ін.), Вогнетривкі наповнювачі, при необхідності, - 3-8% глушників, 1 5% пігментів і органічних барвників. Нефтріттованние емалі отримують помелом (без плавлення) в воді вихідних матеріалів.
Шликер або пудру наносять на попередньо підготовлену (знежирену, протравлену, очищену піском) поверхню металу зануренням, обливом, пульверизацією, електростатичним напиленням, електрофорезом і ін. Способами. Пудру часто завдають напиленням за допомогою вібросит на поверхню, нагріту до 600-800 ° С. Вироби, покриті грунтовій емаллю, сушать в конвеєрної сушарці при 150-180 ° С, після чого наносять покривну емаль. Кожен шар емалі обпалюють окремо в камерних, тунельних і ін. Печах.
Залежно від вихідного складу оксидів і температури випалу емалі бувають легко-і тугоплавкими, в залежності від фазового складу покриття - стеклообразнимі і стеклокристаллических (сіталлізірованнимі). Оптимальні температури випалу емалей для виробів з чавуну і сталі: грунтових - 850-980 ° С, покривних - 800-920 ° С; з алюмінію і його сплавів -530-580 ° С; з благородних і кольорових металів -750-850 ° С; з тугоплавких металів і сплавів - до1600 ° С. Для отримання якісних покриттів розплавлені емалі повинні добре змочувати метал; при цьому в'язкість розплавленої емалі не повинна перевищувати 100 Па x с, а величина її поверхневого натягу - 300 Н / м.
Тривалість випалу покриття 3-4 хвилини для дрібних виробів і до 30-40 хвилин для великих. Звичайна товщина емалі 0,07-0,02мм, в разі товстостінних виробів хімічної апаратури - до 1-2 мм (2-3 шари ґрунтової емалі і до 7 шарів покровной). Наявність великої кількості шарів сприяє релаксації виникають при охолодженні напружень, обумовлених відмінністю температурного коефіцієнта лінійного розширення емалей і металів. Щоб уникнути утворення дефектів ці напруги не повинні перевищувати 50-100 МПа для склоподібних емалей і 150-200 МПа для стеклокристаллических. Готові покриття іноді розписують фарбами на основі забарвлених оксидів або солей металів.
Технічні емалі призначені для збільшення зносостійкості і жаростійкості різних апаратів в хімічній, харчовій і фармацевтичній промисловості, що експлуатуються в агресивних середовищах і при високих температурах. Їх наносять також на вироби побутового призначення (посуд, холодильники, різні види нагрівальних печей та їх елементи, газо і димо відвідних пристроїв), деякі архітектурно-будівельні лицювальні деталі, дорожні знаки тощо.
Емаль відома з глибокої давнини (Др.Егіпет), в Візантії в 10-12 ст. використовувалася при художніх роботах по золоту, на Русі відома з 11 ст. Для покриття виробів технічного призначення застосовують з кінця 17 ст.
Розвиток енергетики, металургії, космонавтики, авіабудування тісно пов'язане з вирішенням завдання створення нових матеріалів конструкційного призначення для роботи в екстремальних умовах - при високих і надвисоких температурах в агресивних середовищах і при ерозійних впливах.
Дослідники і матеріалознавці вирішують цю складну задачу або удосконалюючи наявні конструкційні матеріали шляхом їх легування, оптимізації структури, створення композицій складного складу, або формуючи на поверхні матеріалів функціональні захисні покриття.
Найважливіша властивість високотемпературних матеріалів і покриттів - жаростійкість, тобто здатність протистояти впливу високих температур, в тому числі стійкість до окислення в цих умовах - залежить від цілого ряду чинників. Серед них - хімічний склад і співвідношення вихідних компонентів, їх дисперсність, режим термообробки при формуванні захисного шару, структурний стан компонентів і ін.
Емаль забезпечує, як відомо, виключно ефективний захист від окислення при високих температурах. На рис.1 показана швидкість окислення чистого і емальованого металів на повітрі. Емалеві покриття і композиційний матеріал метал емаль володіють великою мірою винятковими і іноді унікальними споживчими властивостями в порівнянні з іншими покриттями матеріалами, наприклад, пластиками і легованими сталями, причому ці властивості, часто, набагато краще, ніж у названих матеріалів. Захист і облагороджування поверхні визначається такими властивостями, як відсутність пір, гладкість, твердість, стійкість до подряпин і стирання, питомі характеристики якості поверхні, декоративність зовнішнього вигляду, стійкість до дії агресивних середовищ, до дії світла та опромінення.
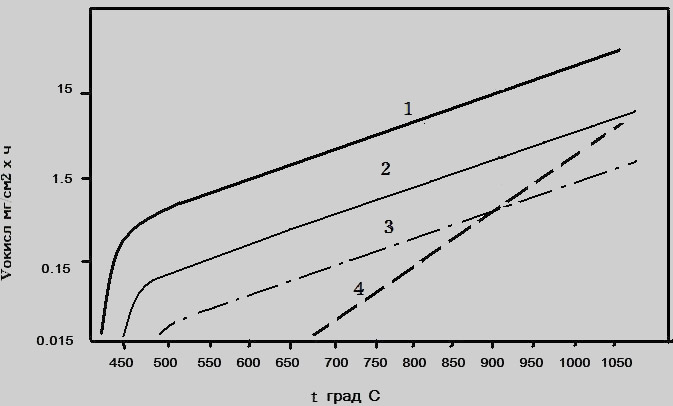
Сюди ж відносяться гігієнічні властивості, фізіологічна нешкідливість і протибактерійні характеристика. Якщо тепер зіставити споживчі властивості емалевого покриття з властивостями легованих сталей і високополімерних матеріалів, то виявиться (згідно з багатьма дослідженнями), що емаль частково перевершує ці матеріали по твердості, щільності, жаро-, атмосферо-, волого-, і кислотно-стійкості, стійкості в миючих засобах, можливість збереження забарвлення, блиску, гігієнічності, здатності до очищення.
Емалеві покриття в теплотехніці піддаються лише помірним температурним навантаженням, Областю їх застосування є, наприклад, сталеві витяжні труби та димоходи, які, повинні надійно протистояти агресивним газам, конденсату та ерозії. Боуше і ін. (1976, 1979, 1981 р.р.) вказують, що стійкість таких покриттів складає 15-20 років.
Високотемпературні емалі захищають метали, наприклад, сталь, ливарний чавун, леговані сталі, жароміцні сплави, мідь або титан від окислення в інтервалі 600-1200 ° С. Про застосування таких емалевих покриттів є чимало інформації в літературі; оглядові статті публікували Петцольд (1960), Аппен, Петцольд (1984), Солнцев (1984).
Приклад захисту металу від окислення емалюванням представлений на рис.2. Емалеві покриття захищають метал від впливу гарячих агресивних газів містять SO2, СО2, або газів містять сірководень і крім того вони захищають від науглероживания і наводоражіванія.
До переваг емалевих покриттів відноситься можливість широкого варіювання складів, що дозволяє отримувати матеріали із заданими властивостями, в яких використовуються кращі якості компонентів.
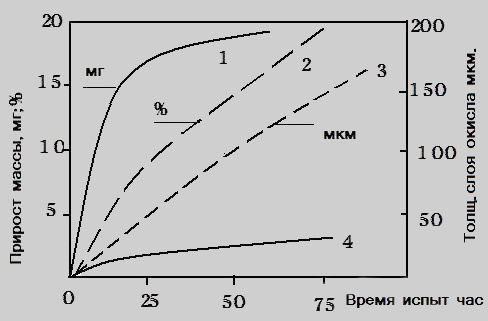
З наведеного графіка наочно видно різницю в корозійної стійкості емальованої сталі, що вигідно відрізняє її в умовах проведених випробувань від стійкості легованих сталей і вже тим більше від незахищеної покриттям вуглецевої сталі. Так товщина окисного шару на сталі AISI 321 (крива 3) після 75 годин витримки при 820 ° С в агресивному газовому середовищі становить понад 150 мкм, що вказує на можливість доведення зразка при його товщині 500 мкм в даних умовах до повного руйнування.