Статичними називаю випробування, при яких додається до зразка навантаження зростає повільно і плавно. До таких випробувань відносять ис-вання на розтяг, стиск, кручення, вигин і визначення твердості. Різні напружені стани, що виникають при тому або іншому методі статичних випробувань, прийнято оцінювати коефіцієнтом жорстко-сті
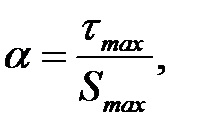
де # 964; тах - найбільше дотичне напруження; Smax - максимальне приве-денное нормальне (розтяжне) напруга.
Чим більше Smax в порівнянні з # 964; тах. тим менше значення # 945; і тим більш жорстке випробування.
Слід мати на увазі, що жорсткість випробувань визначається не тільки коефіцієнтом # 945 ;, а й властивостями того матеріалу, який вико-випробовують.
В даному курсі розглядається тільки випробування на розтягнення - найбільш рас-рення для конструкційних сталей, кольорових металів і їх спла-вів. За одне випробування встановлюється ряд важливих якісних і розрахункових механічних характеристик зразка.
В результаті експерименту отримуємо діаграму розтягування (рисунок 19, а): крива 1 характеризує поведінку (деформацію) металу під дей-наслідком напруг, величина яких є умовною (# 963;), її обчислюють-ляють розподілом навантаження Р в даний момент часу на первинну площа поперечного перерізу зразка F0 (# 963; = P / F0. кгс / мм 2). Крива 2 описує поведінку (деформацію) металу під дією напружень S, величина яких є істинною, її обчислюють діленням навантаження Р в даний момент часу на площу поперечного перерізу зразка в цей же момент. При випробуванні на розтяг зазвичай користуються діа-грамою умовних напружень. Як видно з рис. 1, до точки А деформує-ція пропорційна напрузі. Тангенс кута нахилу прямої Про А до осі абсцис характеризує модуль пружності матеріалу Е = # 963; / # 948; (# 948; - щодо правомірності-кові деформація). Модуль пружності Е визначає жорсткість ма-ла, інтенсивність збільшення напруги в міру пружною деформації.
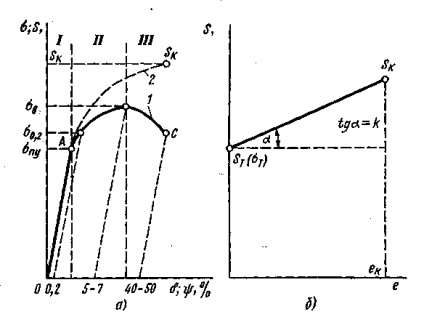
Малюнок 19. Діаграми:
а - розтягування металів для умовних (-) і істинних (- - -) напружень; I - область пружною деформацій; II - область пластичної деформації; III- область раз-витку тріщин; б - справжніх напруг
Фізичний сенс модуля пружності зводиться до того, що він характе-ризует опірність металу пружною деформації, т. Е. Зсуву атомів з положення рівноваги в решітці.
Модуль пружності досить незначно залежить від структури металу і визначається силами міжатомних зв'язку. Всі інші механічного-ські властивості є структурно чутливими і змінюються в зави-ності від структури (обробки) в широких межах.
Напруга, відповідне точці А, називають межею пропорції-нальності (# 963; п.ц.).
Напруги, що не перевищують межі пропорційності, практичні скі викликають тільки пружні деформації, тому нерідко його отождест-вляют з умовним межею пружності (). Це не цілком точно, але прийнятно для багатьох випадків практики. Межа пружності визначається як напруга, при якому залишкова деформація досягає 0,05% (або ще менше) від початкової довжини зразка.
Напруга, що викликає залишкову деформацію, рівну 0,2%, на-викликають умовною межею текучості ().
Межа плинності найчастіше вибирають в якості одного з показате-лей міцності. величини # 963; п.ц і характеризують опір малим і помірним деформацій. Подальше підвищення навантаження викликає більш значну пластичну деформацію в усьому обсязі металу. Напруга, що відповідає найбільшому навантаженню, що передує разруше-нию зразка, називають тимчасовим опором, або межею міцно-сті.
У пластичних металів, починаючи з напруги, що відповідає величині. деформація зосереджується в одній ділянці зразка, де з'являється місцеве звуження поперечного перерізу, так звана шийка. В результаті множинного ковзання і перетину дислокації в шийці утворюється висока щільність вакансій, укрупнення яких призводить до виникнення-ня пір. Зливаючись, пори утворюють тріщину, яка поширюється в напрямку, поперечному осі розтягування, і в певний момент обра-зец руйнується (точка С на малюнку 19, а).
При випробуванні на розтяг визначають, крім того, характеристики пластичності. До них відносяться відносне подовження
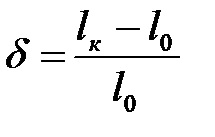
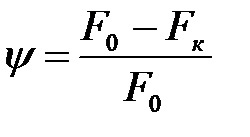
де l0. lк - довжина зразка до і після руйнування; F0 і FK - площа поперечного перерізу зразка до і після руйнування відповідно.
Визначення твер-дости набуло широкого застосування в виробничих-них умовах, представляючи собою найбільш простий і швидкий спосіб визначення й випробування механічних властивостей. Так як для вимірювання твердості відчувають поверхност-ні шари металу, то для отримання правильного резуль-тату поверхню металу не повинна мати зовнішніх дефектів (тріщин, великих подряпин і т. Д.). Існують різні способи випробування на твер-дість. Нижче наведені три, найбільш поширені з них.
Вимірювання твердості методом Брінелля .Сущность це-го способу полягає в тому, що в поверхню іспитуя-мого металу вдавлюється сталевий загартований кульку діаметром 2,5; 5 або 10 мм під дією навантаження со-відповідально 1,87; 7,5 і 30 кН. На поверхні зразка залишається відбиток (рисунок 20, а), по діаметру якого визначають твердість. Діаметр відбитка вимірюють спе-ціальної лупою з поділами. На практиці користуються спеціальними таблицями, які дають переклад диамет-ра відбитка в число твердості, що позначається НВ. Цей спосіб застосовують головним чином для вимірювання твер-дости незагартована металів і сплавів: прокату, поковок і виливків.
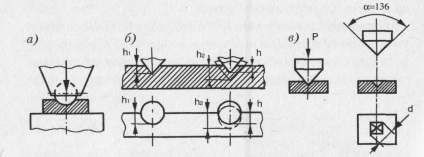
Малюнок 20. Вимірювання твердості методами
Бринелля (а), Роквелла (б) і Віккерса (в)
По твердості, яка вимірюється цим методом, можна су-дить про міцність при розтягуванні, так як між твердо-стю і міцністю існує наступна залежність: sв = (0,34-0,36) НВ для поковок і прокату; sв = (0,3-0,4) НВ для сталевого лиття; SН = 0,12 НВ для сірого чавуну. Та-ким чином, твердість може служити характеристикою міцності властивостей сплаву.
Вимірювання твердості методом Роквелла. Вимірювання здійснюють шляхом вдавлення в випробуваний метал сталевої кульки діаметром 1,59 мм або конусного ал-Мазне наконечника з кутом при вершині 120 ° (рисунок 20, б) .На відміну від методу Брінелля твердість по Роквеллу визначають не по діаметру відбитка, а по глибині вдавлення кульки або конуса.
Вдавлювання проводиться під дією двох по-отже прикладених навантажень - попередню оплату-ної, рівній 98,1 Н, і остаточної (загальною) навантаження, що дорівнює 98,1, 588,6 і 1471,5 Н. Твердість визначають по раз-ності глибин вдавлення відбитків. Для випробування твердих металів необхідна навантаження 1471,5 Н, а вдав-ливание сталевим кулькою навантаженням 98,1 Н виробляють для визначення твердості незагартованої стали, бронзи, латуні та інших м'яких матеріалів. Випробування над-твердих матеріалів виробляють алмазним Наконечний-ком навантаженням 588,6 Н. Глибина вдавлення вимірюється автоматично, а твердість після вимірювання відраховуючи-ється за трьома шкалами: А, В, С. Твердість (число твердо-сти) по Роквеллу позначається наступним чином :
Відлік за шкалою
Визначення твердості за методом Роквелла має широке застосування, так як дає можливість відчувати м'які і тверді метали; розмір відбитків дуже незначний, тому можна відчувати готові деталі без їх псування.
Вимірювання твердості методом Віккерса. Цей метод по-зволяет вимірювати твердість як м'яких, так і дуже твердо-дих металів і сплавів. Він придатний для визначення твердості дуже тонких поверхневих шарів (товщі-ной до 0,3 мм). В цьому випадку в випробуваний зразок вдав-ється чотиригранна алмазна піраміда з кутом при вершині 136 ° (рисунок 20, в). При таких випробуваннях мож-но застосовувати навантаження від 50 до 1200 Н. Вимірювання відбитка виробляють по довжині діагоналі відбитка рассмат-Ріва під мікроскопом, що входять в прилад для визначення твердості. Число твердості по Віккерсу позначають HV, його знаходять за формулою:
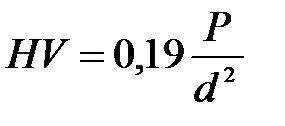
де Р - навантаження, Н;
d - довжина діагоналі відбитка, мм.
На практиці число твердості HVнаходят за таблицями. Крім зазначених методів вимірювання твердості суще-обхідних способи визначення мікротвердості микроско-пическое малих обсягів металу.
В даний час розроблений прогресивний спосіб визначення твердості за допомогою ультразвуку. На малюнку 21 представлена схема ультразвукового твердоміра. Він со-стоїть з перетворювача 1, хвилеводу 2 з індикатором 3, на кінці якого є алмазний наконечник, реєструючого пристрою 4 і генератора 5. наконеч-ник вдавлюється з незначною фіксованою на-вантаженням. Він з'єднаний зі стрижнем, хто вагається з Резо-нансной частотою. Ця частота змінюється в залежності від розміру відбитка алмазного наконечника і характери-зует твердість матеріалу. Розмір відбитка незначний-ний, його не слід визначати під мікроскопом, як в приладі Віккерса і при вимірюванні мікротвердості, незначно пошкоджується поверхню, процес изме ренію твердості може бути автоматизований.
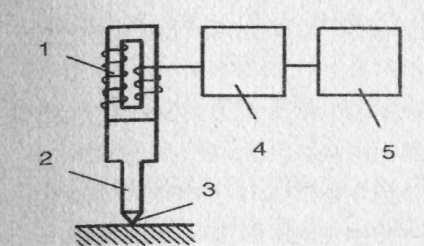
Малюнок 21. Схема пристрою ультразвукового твердоміра
Механічні свойстваопределяют здатність металів чинити опір впливу зовнішніх сил (навантажень). Вони залежать від хімічного складу металів, їх структури, способу технологічної обробки та інших факторів. Знаючи механічні властивості, можна судити про поведінку металу при обробці і в процесі роботи конструкцій і механізмів.
Дано визначення таких понять, як напруга і деформація, пружна і пластична деформації, механізм пластичної деформації, вплив пластичної деформації на властивості металу. Показана методика статичних випробувань на розтяг, визначені основні види напруг. Розглянуто основні способи випробування на твер-дість