Застосуванні матеріалів MASTERTOP® забезпечує зниження експлуатаційних витрат і продовження термінів служби конструкції в 8-10 разів (при правильному дотриманні технології і рецептури).
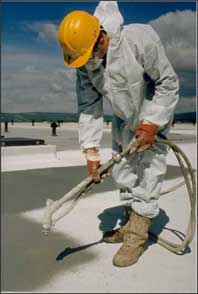
Матеріали MASTERTOP® виробляються більше 70 років підприємствами корпорації Degussa AG - світового лідера з виробництва високотехнологічних матеріалів будівельної хімії (понад 44 тисяч співробітників щорічно створюють і виробляють матеріали на суму понад 11 млрд. Євро). Ці суміші використовувалися при влаштуванні та ремонті промполов площею кілька мільйонів квадратних метрів по всьому світу - від Нової Зеландії до Фінляндії.
ВУкаіни підлоги MASTERTOP® - на заводах «Балтика», «Coca-Cola», «Wrigley», «Philip Morris», підприємствах «Nestle», «Chupa-Chups», в мережі гіпермаркетів «METRO CashCarry».
Чому саме підлоги з МASTERTOP® краще?
Відповідь - в їх характеристиках:
- витримують навантаження аж до траків танків і бульдозерів;
- стійкість до стирання в 4 рази вище, ніж у бетону класу В22,5;
- мають незначне пилеотделеніе;
- електропровідні (електричний опір <25000 Ом);
- вологостійкі;
- стійки до сольовий агресії (зокрема - до Антиожеледний солям);
- витримують температуру не менш 1000С;
- стійки до мінеральних масел, бензину і розчинників (в 3-4 рази вище, ніж у бетону класу В22,5);
- задовольняють найжорсткішим вимогам до промислових підлог (за термінологією СНиП 2.03.13-88 «Підлоги»);
- має 15 кольорів (на вибір).
Результат - зниження експлуатаційних витрат і продовження термінів служби конструкції в 8-10 разів (до 50 років) Але це тільки при дотриманні технології пристрою і правильному підборі матеріалу!
Резонне питання - а як правильно вибрати покриття промислового статі?
Коли на підлоги діє транспортне навантаження від легкого до помірного - у підвалах, механічних цехах, складських приміщеннях, коридорах, гаражах, вантажних платформах, підприємствах з переробки та сортування твердих побутових відходів (ТПВ), тротуарах - застосовується кварцесодержащая суміш MASTERTOP® 100.
Його ми використовували в Череповці, в цеху оцинкування автолиста в ЗАТ «Севергал», на Алчевському заводі з переробки ТПВ «Екопром-Липецьк».
Коли потрібні підлоги з високою стійкістю до стирання і ударних впливів - в механічних цехах, гаражах, цехах складання автомобілів, транспортних шляхах в металургії, авіаційних ангарах, складах з високими навантаженнями, поліграфічних підприємствах, сухих ділянках на целюлозно-паперових комбінатах - застосовується MASTERTOP® 200 з металевими наповнювачами.
Для зміцнення поверхні бетонних підлог у важкій промисловості - при виробництві сталевих канатів, литві металу, складах при зберіганні продукції в високих стелажах, гаражах і ангарах - влаштовується високоміцна стяжка товщиною до 15 мм із застосуванням MASTERTOP® 210 металевими наповнювачами.
При екстремальних транспортних та ударних навантаженнях - для завантажу-розвантажувальних платформ, колій руху важкої гусеничної техніки, виробничих зон сталевої промисловості, перевалочних станцій каменоломень, шахт, сміттєпереробних підприємств, бункерів і тунелів на шахтах і рудниках - влаштовується високоміцна стяжка товщиною до 30 мм із застосуванням MASTERTOP® 230 металевими наповнювачами.
Коли висуваються вимоги щодо антистатичності і електропровідності для захисту від електричного розряду і займання - на підприємствах з виготовлення боєприпасів, лакофарбової, електронної високотехнологічної промисловості, газобензинових заводах, в лабораторіях - застосовується MASTERTOP® 201 з металевими наповнювачами і струмопровідними речовинами.
Коли потрібні підлоги з високою стійкістю до стирання і ударних впливів. високою довговічності, пилеооталківанію і відсутності плям іржі на поверхні - для робочих зон промислових підлог, зон зберігання продукції і шляхів руху важкої техніки в сталевої промисловості, складах з високим навантаженням, в зонах роботи установок на поліграфічних підприємствах -застосовується MASTERTOP® 450 з додаванням корунду.
Для всіх матеріалів MASTERTOP® обов'язковий догляд засобами MASTERKURE® 113 (для натурального кольору), MASTERKURE® 114 (для кольорових покриттів) або MASTERKURE® 620 (для антистатичні підлог MASTERTOP® 201).
Технологія влаштування підлог із застосуванням матеріалів MASTERTOP® включає:
1. Нівелювання підстави.
2. Укладання на існуюче бетонну основу поліетиленової плівки товщиною 0,2 мм.
3. Укладання і закріплення уздовж стін і колон стрічки з еластичного закритоячеістие пінополіетилену товщиною не менше 6 мм.
4. Пристрій арматурного каркаса і установка його на «Чопик».
5. Установку і закріплення напрямних по нівеліру.
6. Приймання бетонної суміші з подачею її з міксерів або бетононасосом.
7. Розподіл бетонної суміші.
8. Розрівнювання бетону. Після ущільнення бетону напрямні можуть бути залишені в бетоні або витягнуті.
9. Для зменшення випаровування вологи з поверхні бетону при несприятливих умовах (протяги, робота в опалювальних приміщеннях в холодну пору року) рекомендується розпорошення MASTERKURE® 111 CF.
10. Зміцнення крайок технологічних і деформа¬ціонних швів.
11. Обробку бетонної поверхні затирочной машиною ( «гелікоптером») з диском.
12. Перше нанесення порошкового упрочнителя MASTERTOP® по поверхні бетону (близько 65% від загального обсягу).
13. Першу затірку MASTERTOP® диском затирочної машини.
14. Друге нанесення порошкового упрочнителя MASTERTOP® по поверхні бетону (близько 35% від загального обсягу).
15. Другу затірку MASTERTOP® диском затирочної машини.
16. Додаткову затірку 1-2 рази (якщо після перших двох ще не відбулося якісного втирання сухої суміші в поверхню бетону).
17. Перше вигладжування поверхні бетону «вертольотом» з лопатами. Проводиться після часткової втрати поверхнею свого блиску і початкового її затвердіння.
18. Наступні вигладжування за 3-5 проходів з поступовим збільшенням кута атаки лопатей затирочної машини до додання поверхні бетону металевого блиску.
19. Нанесення на поверхню бетону матеріалу MASTERKURE® 113 або MASTERKURE® 114 за допомогою валі¬ка або розпилювача.
20. Захист поверхні (укриття на 5-7 діб), щоб уникнути забруднення, зміни кольору або фізичних ушкоджень зміцненої поверхні.
21. Очищення інструментів.
22. Нарізку температурно-усадочних швів (сітка швів не більше 6 м в опалювальному приміщенні), орієнтовно через 24-36 годин після # 61620; 6 закінчення основних робіт.
23. Заповнення технологічних, деформа¬ціонних і температурно-усадочних швів поліуретановим химостойкие герметиком MASTERFLEX® 474 рекомендується проводити через 2 тижні.
Дива А.Г. головний спеціаліст ТОВ «Будівельні системи» (напрям «Промислові підлоги»), кандидат технічних наук