Залежність виходу по току і твердості опадів заліза від швидкості протікання електроліту
Залізнення (осталивание) в більшості випадків застосовують для відновлення розмірів дорогих деталей, а також для отримання корозійно-стійких покриттів. Вирішальним фактором при Залізнення сталевих деталей є міцне зчеплення покриття з основою.
Для зносостійкого залізнення деталей застосовують електроліт (в г / л):
Режим електролізу: температура електроліту 75 -80 ° С, Ік = 3 ÷ 5 А / дм 2. співвідношення Sa: Sк = 1: 1 ÷ 2: 1, аноди - сталеві смуги в чохлах з склотканини марки ТСФ-9л.
У ванні залізнення деталі витримують без струму протягом 10 - 30 з з метою прогріву і руйнування пасивної плівки. Потім підвіску з деталями встановлюють на катодного штанзі при Ік = 3 ÷ 5 А / дм 2. і протягом 10 хв значення Ік доводять до розрахункової (10 - 20 А / дм 2). Після осталивание деталі промивають в гарячій воді, нейтралізують в 5- 10% -ому розчині каустичної соди і знову промивають в гарячій воді.
Кислотність електроліту коригують з урахуванням того, що за 1 А / ч витрачається 0,8 г кислоти.
Для зносостійкого залізнення застосовують електроліт з рН = 0,1, що містить FeCl2 • 4H2 O (450-500 г / л). Режим електролізу: температура електроліту 40 80 ° С, Ік = 5 ÷ 20 А / дм 2. аноди сталеві.
З підвищенням температури зменшується наводоражіваніе і збільшується вихід за струмом газоподібного водню, що виділяється у вигляді бульбашок на катоді. З ростом температури збільшуються розміри області когерентного розсіювання, зменшується щільність дислокації і розміри мікроіскаженій покриттів заліза.
Незважаючи на те, що водневе перенапруження знижується з ростом температури, наводоражіваніе осаду зменшується, що пов'язано зі зміною адсорбції водню на поверхні зростаючих кристалів. З підвищенням температури блокуючий вплив водню зменшується, розміри когерентного розсіювання збільшуються, а щільність дислокацій і мікроіскаженія зменшуються. Іншою причиною, що полегшує умови формування осаду, є зменшення перенапруги для заліза з підвищенням температури.
Збільшення Ік сприяє зменшенню наводоражіванія. Зі збільшенням рН зменшується вихід за струмом газоподібного водню, що пов'язано зі зменшенням концентрації іонів гідроксилу у катода. Таким чином, водень є одним з основних факторів, що впливають на формування осаду, і перешкоджає росту кристалів, подрібнюючи субмікроструктуру.
Перспективним є проточное осталивание деталей в електроліті, що містить 650 г / л хлористого заліза при 80 ° С. Швидкість протікання електролізу в просторі між анодом і катодом складає <15 см/с. Концентрация соляной кислоты равна 2-2,5 г/л, iк = 40 ÷ 60 А/дм 2. расстояние между анодом и катодом составляет 2,5 мм.
На катодний поляризацію істотно впливає швидкість протікання електроліту (рис. 26). З проточного електроліту осадження заліза відбувається при бо'льшую позитивних значеннях потенціалу, ніж в непроточних. Причиною цього служить зменшення защелачивания прікатодном шару, що призводить до зменшення кількості утворюється гідроксиду заліза і створення умов для більш інтенсивного розряду іонів заліза і застосування більш високої щільності струму.
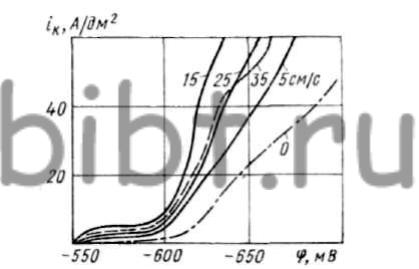
Мал. 26. Залежність катодного поляризації (2,56 г / л НСl) від швидкості протікання електроліту
Зі збільшенням швидкості руху електроліту від 0 до 5 см / с середній вихід по току зростає до 97,6% проти 87,9% в стаціонарних умовах (рис. 27). Зі зміною швидкості руху електроліту від 5 до 25 см / с твердість покриття становить 440 - 500 кгс / мм 2 і максимальна при 25-35 см / с. При стаціонарному режимі і Ік = 20 А / дм 2 твердість дорівнює 300 - 400 кгс / мм 2.
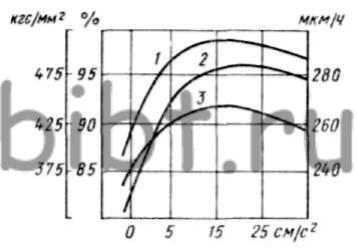
М'які і блискучі покриття залізом застосовують в деяких випадках як подслой під кобальт, нікель або хром. Найбільше використання знайшов для цієї мети електроліт (в моль / л)
Режим електролізу: температура електроліту 18-30 ° С, Ік = 1 ÷ 3 А / дм 2. аноди - з заліза. Мікротвердість таких опадів 280 - 320 кгс / мм 2. Катодний вихід покриття залізом становить 93-95%, а анодний 100%; рН електроліту має підтримуватися в межах 2,7 - 2,9.
У процесі електролізу на аноді можливо окислення Fe 2+ до Fe 3+. що викликає плямистість або почорніння катодних опадів і появу на аноді легко знімається шламу, тому аноди слід поміщати в чохли з хлорину або склотканини. Найкращі результати отримують при використанні анодів з армко-заліза або сталі, що містить не більше 1% вуглецю.
Не менш перспективним для блискучого залізнення є електроліт (в г / л):
Миючий засіб «Прогрес», мл / л 0,4
Режим електролізу: температура електроліту 18-20 ° С, Ік = 4 ÷ 10 А / дм 2. аноди з армко-заліза, рН = 1,65.
Перемішування електроліту стисненим повітрям неприпустимо, так як це призводить до окислення. Мікротвердість покриттів, одержуваних при Ік = 2 ÷ 5 А / дм 2. становить 220 - 250 кгс / мм 2. а блиск 60-70%.
Петро Степанович Мельников. Довідник по гальванопокриття в машинобудуванні. Тисяча дев'ятсот сімдесят дев'ять.