Лапицкий Галина Олександрівна. викладач
Тайгінскій інститут залізничного транспорту - філія ФГБОУ ВО "Омський державний університет шляхів сполучення"
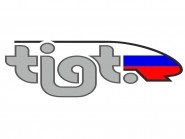
Використовувані методи неруйнівного контролю в даний час реалізовані переважно у вигляді технологій ручного контролю, а це обмежує продуктивність і пред'являє досить високі вимоги до кваліфікації персоналу.
Перспективними напрямками науково-дослідних і дослідно-конструкторських робіт в галузі неруйнівного контролю та технічної діагностики при виготовленні і ремонті відповідальних улов і деталей слід вважати впровадження автоматизованих систем і комплексів, де використовуються різні методи неруйнівного контролю та технічної діагностики із застосуванням мікропроцесорної і комп'ютерної техніки.
В системі технічного діагностування локомотивів використовуються методи, засоби, системи і технологічні прийоми діагностики, що базуються на ряді понять і визначень, встановлених державними стандартами. Діагностування - процес встановлення ознак, що характеризують технічний стан об'єктів (локомотивів, дизель-поїздів), а також його будь-якого елементу, за зовнішніми ознаками або параметрам з певною точністю зазначення місця, виду і причин дефекту, якщо такий виявлений [1].
Засобами діагностування є:
-стаціонарні комп'ютери, з унікальним програмним забезпеченням, що дозволяють діагностувати контрольовані параметри, обробляти і представляти інформацію в цифровому і графічному вигляді;
-мобільні комп'ютери, ноутбуки, що дозволяють діагностувати контрольовані параметри, обробляти і представляти інформацію в цифровому і графічному вигляді;
-стаціонарні вимірювальні прилади;
-мобільні вимірювальні прилади;
-механізовані робочі місця для розбирання і складання агрегатів і вузлів, що надійшли в ремонт;
-стендове обладнання для обкатки, випробування і налаштування агрегатів, вузлів;
-обладнання для балансування обертових елементів машин;
-камери і машини для обдування і миття агрегатів, вузлів і деталей перед ремонтом;
-камери для фарбування, сушіння агрегатів, вузлів і деталей;
-обладнання для демонтажу і монтажу агрегатів і вузлів рухомого складу;
-обладнання для спільної притирання деталей і ін. [2].
Як приклад інноваційних технологій варто назвати такі розробки ВАТ «НІІТКД», як: комплекс інтелектуальний виробничий автоматизований реостатних випробувань тепловозів «КИПАРИС-5», апаратно-програмний комплекс АПК «БОРТ», стендове обладнання для сервісного обслуговування «БОРТ», система контролю і діагностики (СКД) «Доктор-030М».
«КИПАРИС-5» є виробом нового покоління. Призначений для діагностування, контролю параметрів, обробки та подання інформації в цифровому і графічному вигляді; видачі рекомендацій і вказівок по налаштуванню параметрів дизель-генераторних установок (ДГУ) магістральних і маневрових тепловозів серій 2ТЕ10, 2ТЕ116, 2ТЕП70, М62, ТЕМ2, ТЕМ7, ТЕМ18, ЧМЕ3 при проведенні реостатних випробувань в умовах СЛД і ремонтних заводів.
Комплекс дозволяє проводити оцінку технічного стану дизель-генераторної установки тепловоза при мінімальному демонтажі його обладнання, не викликати перевищення планових норм простою на ремонті і самих реостатних випробуваннях, встановлювати оптимальні, з точки зору надійності і економічності, режими роботи ДГУ в експлуатації за рахунок більш раціональної настройки систем і агрегатів тепловоза і т.п.
На підставі експертних оцінок «КИПАРИС-5» ремонтному персоналу цехів і відділень видаються рекомендації щодо усунення зазначених несправностей ДГУ тепловоза і автоматичної системи регулювання потужності. Дієвим елементом підвищення якості ремонту є післяремонтний (вихідний) контроль технічного стану тепловоза.
АПК «БОРТ» дозволяє перейти з прогнозованого нормування палива, заснованого на середньостатистичних показниках, на сучасний метод нормування по реально виконану роботу, з урахуванням технічного стану тепловоза, який базується на отриманих даних комплексу.
Система дає можливість об'єктивно нормувати витрата дизельного палива, виключити несанкціоновані сливи палива, на основі отриманих даних робити висновки про роботу паливної апаратури і про обсяг роботи, виконуваної тепловозом за певний період; відслідковувати час руху, гарячого простою, заглушеного стану, роботи тягового генератора; побачити реальний пробіг тепловоза і т.д. [3].
Система контролю і діагностики (СКД) «Доктор-030М» призначена для вимірювання активного опору постійному струму, індуктивності, тимчасових інтервалів спрацьовування електрокоммутаціонной апаратури; вимірювання опору навантаження низьковольтних ланцюгів, коефіцієнтів трансформації електричних машин постійного струму і трансформаторів, а також видачі напруги постійного і пульсуючого струму, використовуваних для діагностування і настройки електричних ланцюгів, вузлів і апаратів локомотивів.
За допомогою СКД експрес-контроль обладнання проводиться протягом 20 ÷ 30 хвилин з подальшим виявленням несправних вузлів і агрегатів і подальшої їх локалізацією. СКД дозволяє вимірювати параметри електричних апаратів, проводити обробку і виведення результату на вбудований рідкокристалічний екран дисплея, принтер, а також накопичувати і передавати дані про технічний стан рухомих одиниць в єдину базу даних діагностичних пристроїв для їх подальшої обробки та визначення обсягів ремонту тягових рухомих одиниць.
Перелік параметрів електричних машин і апаратів, що перевіряються СКД «Доктор-030М»:
-межвитковое замикання якорів і обмоток збудження двигунів;
-стан і установка щіток на геометричної нейтрали в електричних машинах постійного струму;
-стан якірного ланцюга і обмоток збудження;
-межвитковое замикання котушок реле, контакторів і інших магнітних систем;
-час спрацьовування комутаційної апаратури;
-перехідний опір контактів контакторів і реле;
-перевірка секвенції включення апаратів від контролера машиніста, «експрес діагностика» - локалізація відхилення параметрів електричних ланцюгів в цілому [4].
Практикою визначено такі види технічної діагностики локомотивів:
-за призначенням - технічна діагностика може бути спеціалізованої й сполученої з плановими обслуговуваннями і ремонтами;
-з технологічного устаткування - діагностика проводиться спеціалізованими пристроями або основними приладами;
-по режиму проведення - планова діагностика проводиться в разі потреби;
-за місцем у системі технічного обслуговування - на потокової лінії комплексної технічної діагностики при визначенні стану або заключна перевірка після виконаного ремонту;
-за типом застосовуваних засобів діагностування - на стаціонарних пунктах, за допомогою бортових систем, переносними засобами.
Для отримання інформації про стан тієї чи іншої частини елементів або протікають процеси може вивчатися будь-яка частина цих елементів. Тепловоз, наприклад, має кілька параметрів, що характеризують якість його функціонування. Такими параметрами, в першу чергу, є потужність при встановленій частоті обертання колінчастого вала і економічність. Тому діагностування починають з контролю саме цих функціональних параметрів. У разі відхилення функціонального параметра від нормального значення необхідно проконтролювати функціональні параметри його підсистем і оцінити їх технічний стан [1].
Для контролю за технічним станом тепловозного парку в процесі експлуатації крім самої системи технічного діагностування необхідно створення систем ведення баз даних з обліку статистики проведення діагностування та результатів вимірювання параметрів обладнання. Крім виконання облікових функцій, подібна система може забезпечити прогнозування технічного стану обладнання. При реалізації прогнозування технічного стану обладнання тепловозів в експлуатації можливий перехід від системи технічного обслуговування з напрацювання (пробігу, часу) до обслуговування по реальному технічному стану. Застосування інноваційних технологій дозволить дати значний економічний ефект за рахунок ліквідації непотрібних ремонтних робіт і вилучення тепловозів з експлуатації, тобто формування обсягу технічного обслуговування індивідуально для кожного тепловозного складу за результатами діагностичного обстеження [5].
Ремонт за технічним станом передбачає визначення обсягів відновлення на основі даних технічної діагностики, що проводиться з встановленою періодичністю. За результатами діагностики приймається рішення про справний і несправному станах, визначається залишковий ресурс працездатності, що забезпечує належну надійність і безпеку в експлуатації. Якщо залишковий ресурс не задовольняє вимогам надійності та безпеки, то приймається рішення про заміну або ремонті, але тільки в строго необхідних обсягах.
Така система обслуговування охоплює вузли і агрегати, конструкція яких, а також можливості технічних засобів неруйнівного контролю, дозволяє забезпечити ресурс до наступного регламентує діагностування або ремонту.
Широкому поширенню і впровадженню системи ремонту за технічним станом перешкоджає відсутність необхідної бази даних, засобів контролю і діагностики з високою вірогідністю технічних прогнозів. Вже сформовані конструктивні особливості рухомого складу, які базуються на застарілих технічних рішеннях, також перешкоджають широкому застосуванню цієї системи ремонту.
Система ремонту за технічним станом відрізняється високою капіталоємністю. Необхідні нові технічні рішення при виготовленні рухомого складу, які забезпечать її застосування. Треба створювати такі конструкції рухомого складу, які забезпечать застосування надійних інноваційних способів діагностики і її доступ до відповідальних вузлів.
Ця система вимагає значних капіталовкладень на розробку способів діагностики, створення, виготовлення і придбання відповідних технічних засобів. Також необхідне спеціальне обладнання робочих місць і ремонтних цехів, розробка і впровадження системи визначення обсягів ремонтних робіт. Важливо також створити банк даних про технічний стан практично всіх відповідальних вузлів і деталей рухомого складу для відповідного корегування оцінок з метою підвищення надійності і безпеки руху [6].
На закінчення хотілося б підкреслити, що найважливішим напрямком удосконалення систем неруйнівного контролю та технічної діагностики як при виготовленні, так і при ремонті і обслуговуванні відповідальних вузлів і деталей локомотивів - базою для підвищення їх достовірності та продуктивності, тобто ефективності, є створення та впровадження нових методик .
Всі поля є обов'язковими для заповнення
Інформація доступна тільки для зареєстрованих користувачів.
Шановні колеги. Переконливе прохання бути уважнішими при оформленні заявки. На підставі заповненої форми оформляється електронне свідоцтво. У разі невірно вказаних даних організація відповідальності не несе.