Для виконання технологічної операції необхідно попередньо провести наладку або настройку технологічної системи.
Під налагодженням технологічної системи розуміють готовність технологічного обладнання і технологічної оснастки до виконання технологічної операції. Налагодження системи являє собою приведення її в робочий стан, придатний для виконання операції або технологічного процесу. У загальному випадку налагодження включає в себе установку ріжучого інструменту, заготовки, робочих органів верстата в положення, яке з урахуванням явищ, що відбуваються в процесі обробки, забезпечує точність заданого розміру. У наладку включається так само установка режимів обробки, установка і перемикання швидкостей і подач, установка інструментів в інструментальні магазини і револьверні головки, установка програмного носія в пристрій, що зчитує верстата з ЧПУ та ін.
Спочатку досягнута точність при налагодженні верстата в процесі роботи поступово втрачається внаслідок дії систематично змінюються чинників, що викликає необхідність її періодичного відновлення. Процес відновлення первісної точності називається процесом підналагодження або поднастройкі технологічної системи. Під підналагодженням розуміють додаткове регулювання технологічного обладнання та (або) технологічного оснащення при виконанні технологічної операції з метою відновлення заданих при налагодженні необхідних параметрів. Підналагоджує може проводитися періодично або безперервно, вручну або автоматично за допомогою різних засобів і пристроїв. При всіх видах налагодження і підналагодження застосовують різні методи досягнення необхідної точності. Завданням налагодження є забезпечення можливості отримання максимальної кількості придатних деталей до першої підналагодження. Для цього необхідно правильно розмістити можливе поле розсіювання, зумовлене дією випадкових і систематичних похибок в заданому полі допуску. Незадовільна налагодження призводить до зміщення кривої розподілу відносно заданого допуску Т і є основною причиною появи браку і частих поднастроек системи (рис. 74).
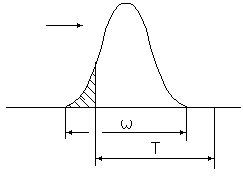
Для підвищення точності обробки і виключення шлюбу проводиться розрахунок налагодження на точність, а її виконання контролюється. При розрахунках точності обробки точність налагодження приймається по табличних даних з урахуванням розмірів заготовки і виду обробки або визначається розрахунком за формулами.
Для поверхонь обертання:
для плоских поверхонь:
З урахуванням похибки зсуву відповідно:
Похибка регулювання визначається похибкою вимірювання, що застосовується регулювального пристрою. Наприклад, при регулюванні по лімбу рег становить від 5 до 70 мкм, по індикатору - 10-20 мкм, по індикаторному упору - 1-15 мкм, за жорстким упору - 20-30 мкм.
При використанні мірних інструментів (свердла, зенкери, розгортки) похибка настройки визначається допусками на виготовлення даних інструментів. У разі багатоінструментальною обробки налагодження верстатів ускладнюється і в ряді випадків доцільно проводити налаштування по раніше обробленої деталі або еталону.
Налаштування верстата на отримання заданого розміру проводиться двома методами: пробних ходів і автоматичного отримання розмірів. У загальному випадку похибка настройки або наладки може прийматися рівною двом середнім квадратичним або 1/10 допуску на розмір.
Необхідність підналагодження виникає в тому випадку, якщо внаслідок дії систематичної похибки витримується розмір виходить за межі допуску. Відновлення первісної точності, викликаної зносом інструменту досягається методом повної або неповної взаємозамінності. Зносився різець замінюється новим, який налаштовується поза верстата в спеціальному пристосуванні, а потім встановлюється на верстаті в необхідне положення. При використанні методу регулювання в розмірну ланцюг вбудовуються спеціальні пристрої для плавного і точного переміщення інструменту в міру його зносу: рухливі супорти, резцедержатели і так далі.
Контроль оброблюваних і оброблених деталей може проводитися за допомогою засобів активного контролю. Регулювання за допомогою засобів активного контролю проводиться в тому випадку, якщо груповий середній розмір деталі або розмір окремої деталі наближається до контрольних кордонів. Засоби активного контролю діляться на два види: застосовувані в процесі обробки і після обробки деталі. При контролі в процесі обробки проводиться безперервний контроль розміру і при виникненні відхилень проводиться або зміна режимів, або положення інструменту, або зупинка верстата. У цьому випадку вдається компенсувати температурні і силові фактори. Засоби активного контролю, що застосовуються після обробки деталі, звуться подналадчіков. За результатами вимірювань обробленої деталі подається команда або сигнал на поднастройкі інструменту. Найбільш раціонально застосування активного контролю при необхідної високої точності і великий серійності виробництва, а так само при малій розмірної стійкості інструменту і високих температурах.
Під час прийому обробку однієї заготовки в якості настроечного розміру приймається середній розмір, який визначається без обліку систематично змінюються похибок:
Налаштування в цьому випадку проводиться за методом пробних ходів.
Під час прийому обробку партії заготовок необхідно розмістити так майбутнє поле рассеяніяТ, обумовлене дією випадкових похибок в заданому полі допуску на механічну обробку, щоб забезпечити можливість обробки максимальної кількості деталей до першої поднастройкі, тобто більшу частину поля допуску залишити для компенсації систематично змінюються похибок . Як настроечного розміру приймається розмір, що зв'язує середину поля допуску ТТ. призначеного для компенсації випадкових похибок, з початком відліку розмірів, якщо застосовується нормальний закон розподілу випадкових похибок. В цьому випадку настроювальний розмір визначається:
де A найменувань - найменший граничний розмір;
а - частина поля допуску, призначена для компенсації систематичних постійних похибок (похибки вимірювання);
3SТ - половина поля допуску для компенсації випадкових похибок Т.
Розглянемо схему побудови настроечного розміру (рис. 75).
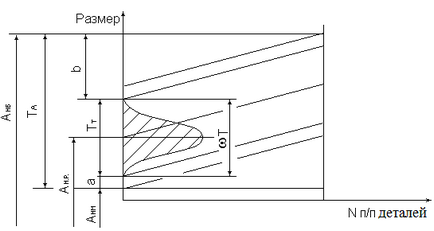
Тут b - частина поля допуску для компенсації систематично змінюються похибок.
Для отримання настроечного розміру необхідно провести обробку пробної партії заготовок і за середнім групового розміром можна судити про правильність настройки.