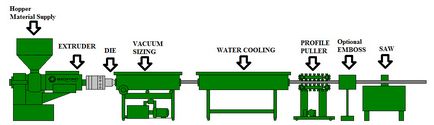
Близько половини вироблених термопластів переробляються в вироби цим способом. Екструзією отримують плівки, листи, труби, шланги, капіляри, прутки, сайдинг, різні за складністю профілі, наносять полімерну ізоляцію на дроти, виробляють багатошарові різноманітні за конструкцією і поєднанню застосовуваних пластмас гібридні погонажні вироби. Переробка вторинних полімерів і гранулювання також виконуються із застосуванням екструзійного обладнання.
Основним обладнанням екструзійного процесу є черв'ячний екструдер, оснащений формуючої головкою. У екструдері полімерний матеріал розплавляється, пластикується і потім нагнітається в головку. Найчастіше використовуються різні модифікації одно- і двухчервячних екструдерів.
Іноді при переробки пластмас застосовуються бесшнековие, або дискові, екструдери, в яких робочим органом, продавлюється розплав в голівку, є диск особливої форми. Дискові екструдери застосовуються, коли необхідно отримати покращене змішання компонентів суміші. Через неможливість розвивати високий тиск формування такі екструдери застосовуються для отримання виробів з відносно невисокими механічними характеристиками і низькою точністю геометричних розмірів.
Комбіновані екструдери мають в якості робочого органу пристрій, що поєднує шнекову і дискову частини, і називаються червячно-дисковими. Застосовуються для забезпечення гарного змішувального ефекту, особливо при переробці композитів. На них переробляються розплави пластмас, мають низьку в'язкість і досить високу еластичність.
Процеси, що відбуваються при екструзії.
Мал. 1. Схема одношнекового екструдера: 1 бункер; 2 шнек; 3 циліндр; 4 порожнину для циркуляції води; 5 нагрівач; 6 решітка з сітками; 7- формуюча головка.
Технологічний процес екструзії складається з послідовного переміщення матеріалу обертовим шнеком в його зонах (див. Рис. 1): харчування (I), пластикации (II), дозування розплаву (III), а потім просування розплаву в каналах формуючої головки.
Розподіл шнека на зони I-III здійснюється за технологічною ознакою і вказує на те, яку операцію в основному виконує дану ділянку шнека. Поділ шнека на зони умовно, оскільки в залежності від природи переробляється полімеру, температурно-швидкісного режиму процесу та інших факторів початок і закінчення певних операцій можуть зміщуватися вздовж шнека, захоплюючи різні зони або переходячи з однієї ділянки в інший.
Циліндр також має певні довжини зон обігріву. Довжина цих зон визначається розташуванням нагрівачів на його поверхні і їх температурою. Межі зон шнека I-III і зон обігріву циліндра можуть не збігатися.
Розглянемо поведінку матеріалу послідовно на кожному етапі екструзії.
Завантаження сировини. Вихідна сировина для екструзії, що подається в бункер, може бути у вигляді порошку, гранул, стрічок. Рівномірний дозування матеріалу з бункера забезпечує хорошу якість екструдата.
Переробка полімеру у вигляді гранул - найкращий варіант харчування екструдера. Це пояснюється тим, що гранули полімеру менше схильні до утворення «склепінь» в бункері, ніж порошок, отже, виключаються пульсації потоку на виході їх екструдера.
Завантаження межвиткового простору під лійкою бункера відбувається на відрізку довжини шнека, що дорівнює (1 - 1,5) D. При утворенні «склепінь» на стінках бункера харчування шнека матеріалом припиняється. Для усунення цього необхідно в бункер поміщати ворошителя.
Сипучість матеріалу залежить у великій мірі від вологості: чим більше вологість, тим менше сипкість. Тому матеріали повинні бути спочатку підсушені.
Для збільшення продуктивності машини гранули можна заздалегідь підігріти.
Застосовуючи пристосування для примусової подачі матеріалу з бункера на шнек, також вдається істотно підвищити продуктивність машини (в 3-4 рази). При ущільненні матеріалу в межвиткового просторі шнека витіснений повітря виходить назад через бункер. Якщо видалення повітря буде неповним, то він залишиться в розплаві і після формування утворює в виробі порожнини, що є браком виробів.
Зміна рівня заповнення бункера матеріалом по висоті також впливає на повноту заповнення шнека. Тому бункер забезпечений спеціальними автоматичними рівнемірами, по команді яких відбувається завантаження бункера матеріалом до потрібного рівня. Завантаження бункера екструдера здійснюється за допомогою пневмотранспорту.
При тривалій роботі екструдера можливий перегрів циліндра під лійкою бункера і самого бункера. В цьому випадку гранули почнуть злипатися і припиниться їх подача на шнек. Для запобігання перегріву цієї частини циліндра в ньому робляться порожнини для циркуляції охолоджуючої води (див. Рис. 1, поз. 4).
Зона харчування (I). Вступники з бункера гранули заповнюють межвитковое простір шнека зони I і ущільнюються. Ущільнення і стиснення гранул в зоні I відбувається, як правило, за рахунок зменшення глибини нарізки h шнека. Просування гранул здійснюється внаслідок різниці значень сили тертя полімеру про внутрішню поверхню корпусу циліндра і об поверхню шнека. Оскільки поверхня контакту полімеру з поверхнею шнека більше, ніж з поверхнею циліндра, необхідно зменшити коефіцієнт тертя полімеру про шнек, так як в противному випадку матеріал перестане рухатися уздовж осі шнека, а почне обертатися разом з ним. Це досягається підвищенням температури стінки циліндра (нагріванням) і зниженням температури шнека (шнек охолоджується зсередини водою).
Нагрівання полімеру в зоні I відбувається за рахунок диссипативного тепла, що виділяється при терті матеріалу і за рахунок додаткового тепла від нагрівачів, розташованих по периметру циліндра.
Іноді кількість диссипативного тепла може бути достатнім для плавлення полімеру, і тоді нагрівачі відключають. На практиці таке відбувається рідко.
При оптимальній температурі процесу полімер спресований, ущільнений і утворює в межвиткового просторі тверду пробку (див. Рис. 2). Найкраще, якщо така змінна пробка утворюється і зберігається на кордоні зон I і II. Властивості пробки багато в чому визначають продуктивність машини, стабільність транспортування полімеру, величину максимального тиску і т. Д.
Мал. 2. Схема плавлення пробки матеріалу в зоні II в межвиткового перетині шнека: 1 стінки циліндра; 2 гребінь шнека; 3 потоки розплаву полімеру; 4 спресований твердий полімер (пробка) в екструдері.
Зона пластикации і плавлення (II). На початку зони II відбувається Підплавлення полімеру, що примикає до поверхні циліндра. Розплав поступово накопичується і впливає на спадаючу по ширині пробку. Оскільки глибина нарізки шнека зменшується в міру просування матеріалу від зони I до зони III, то виникає тиск змушує пробку щільно притискатися до гарячої стінці циліндра, відбувається плавлення полімеру.
У зоні пластикации пробка плавиться також і під дією тепла, що виділяється внаслідок внутрішнього, в'язкого тертя в матеріалі в тонкому шарі розплаву (поз. 3 на рис. 2), де відбуваються інтенсивні зсувні деформації. Остання обставина призводить до вираженого змішувального ефекту. Розплав інтенсивно гомогенізується, а складові композиційного матеріалу перемішуються.
Кінець зони II характеризується розпадом пробки на окремі фрагменти. Далі розплав полімеру із залишками твердих частинок потрапляє в зону дозування.
Основний підйом тиску P розплаву відбувається на кордоні зон I і II. На цьому кордоні утворюється пробка з спресованого матеріалу як би ковзає по шнеку: в зоні I це твердий матеріал, в зоні II- плавиться. Наявність цієї пробки і створює основний внесок в підвищення тиску розплаву. Також збільшення тиску відбувається за рахунок зменшення глибини нарізки шнека. Запасеної на виході з циліндра тиск витрачається на подолання опору сіток, течії розплаву в каналах головки і формування виробу.
Зона дозування (III). Просування гетерогенного матеріалу (розплав, частинки твердого полімеру) продовжує супроводжуватися виділенням внутрішнього тепла, яке є результатом інтенсивних зсувних деформацій в полімері. Розплавлена маса продовжує гомогенізований, що проявляється в остаточному плавленні залишків твердого полімеру, усередненні в'язкості і температури розплавленої частини.
У межвиткового просторі розплав має ряд потоків, основними з яких є поздовжній і циркуляційний. Величина поздовжнього (уздовж осі шнека) потоку визначає продуктивність екструдера Q, а циркуляційного - якість гомогенності полімеру або змішування компонентів.
У свою чергу поздовжній потік складається з трьох потоків розплаву: прямого, зворотного і потоку витоків.
Прямий потік викликаний рухом шнека в напрямку формуючої головки. Зворотний потік - це уявне протягом, яке викликається високим тиском з боку головки; в реальності не існує. Потік витоку відбувається при перетікання розплаву між циліндром і гребенем черв'яка.
Продуктивність Q екструдера з урахуванням розподілу швидкостей різних потоків становить
Q = Qпр - Qобр - Qут,
де Qпр, Qобр, Qут - продуктивності екструдера від прямого потоку, протитечії і витоків розплаву відповідно.
Q = αn - β • (ΔP) / (μ • L),
де n - частота обертання шнека; ΔP - тиск на виході з шнека (в кінці зони III); μ - ефективна в'язкість розплаву; L - довжина шнека; α - константа швидкості прямого потоку, β - константа швидкості зворотного потоку, які залежать від геометричних параметрів шнека.
Основні параметри процесу екструзії. До технологічних параметрів належать температура переробки полімеру, тиск розплаву, температура зон головки і температурні режими охолодження сформованого екструдата.
При занадто високій в'язкості розплаву отримувати вироби методом екструзії важко через великий опір течією розплаву, виникнення нестійкого режиму руху потоку. Все це призводить до утворення дефектів виробів.
Підвищення температури переробки може привести до термодеструкції розплаву, а збільшення тиску, потужності приводу при більш низьких температурах - до механодеструкція, тобто для екструзії розплавів повинні застосовуватися полімери з досить вузьким інтервалом коливання в'язкості.
Основними технологічними характеристиками одношнекового екструдера є L, D, L / D, швидкість обертання шнека n, геометричний профіль шнека (див. Рис.3) і ступінь стиснення (компресії) - відношення обсягу одного витка черв'яка в зоні завантаження до обсягу одного витка в зоні дозування.
Мал. 3. Схема зонної конструкції шнека
Короткошнековие екструдери мають L / D = 12-18, длінношнековие L / D> 30. Найбільш поширені екструдери з L / D = 20-25.
Показником роботи екструдера є його ефективність-відношення продуктивності до потужності споживання.
Матеріали. Більшість термопластів і композицій на їх основі можуть перероблятися екструзією. Для цього достатньо, щоб час перебування розплаву в екструдері при даній температурі було менше часу термостабильности полімеру при тій же температурі. Найбільш широко застосовується екструзія великотоннажних полімерів наступних типів. ПЕ, ПП, ПС ПК ПА, ПВХ (пластифікований і непластифікований), ПЕТФ а також суміші з неорганічними і полімерними наповнювачами і більш складні композиції на їх основі.
Для екструзії застосовуються матеріали та режими переробки при яких ПТР змінюється в межах 0,3 - 12 г / 10 хв, тому що з маловязких розплавів неможливо отримати суцільну екструзійну заготовку у вигляді плівки, труби, профілю. Якщо ж використовуються ливарні марки полімеру, то з них можна отримати екструзією лише окремі типи виробів, так як ПТР у них знаходиться в межах 0,8 - 20 г / 10 хв.
Так, труби, кабельні покриття виробляють з розплаву полімеру з ПТР від 0,3 до 1 г / 10 хв. Це пов'язано з вибором полімеру великої молекулярної маси. Остання визначає експлуатаційні властивості виробів - підвищені фізико-механічні характеристики.
Плівки, листи виготовляють екструзією розплаву з ПТР в межах 1 - 4 г / 10 хв.
Дискретні вироби, вироблені екструзією розплаву з подальшим роздуванням в формі, отримують з розплаву з ПТР = 1,5 - 7,0 г / 10 хв.
Ламінування за допомогою екструзії відбувається при ПТР розплаву в межах 7 - 12 г / 10 хв.
Вироби. Всі вироби, що отримуються на основі термопластів методом екструзії, можуть мати в принципі необмежену довжину. Діаметр виробів обмежується головним чином діаметром шнека екструдера. Чим більше D. тим ширше, товщі можуть виходити вироби.
За матеріалами сайту: Полімерні матеріали